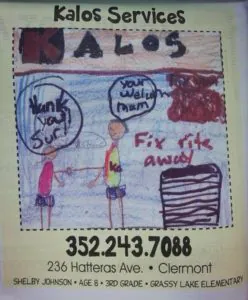
Our Updates
Uncategorized Content
It’s Elementary at Kalos Services, Inc. – 352-243-7088
Thank you, Shelby and Grassy Lake Elementary! Kalos Services, Inc. was so excited to receive
Thank you, Shelby and Grassy Lake Elementary! Kalos Services, Inc. was so excited to receive